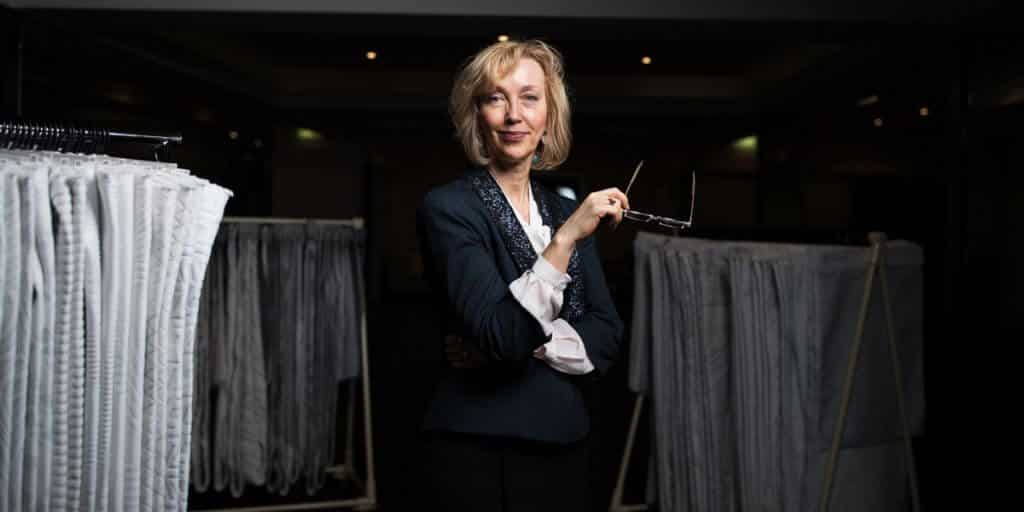
Spend a day at Sealy HQ and be prepared to be surprised. Even though Sealy’s mattresses are sold nationwide at nearly every major retailer, you don’t get the feeling that the company is in the business of ‘mass production’. Rather, the opposite impression is likely to take hold because at Sealy, attention is paid to the details; luxury is woven into every design choice and each bed is made in Australia, by hand.
Consider this statistic: each Sealy bed will pass through 11 sets of hands, minimum. ‘End-to-end attention’ is a hallmark that the company prides itself on. Every detail — from design and research to prototypes and new product launches — are personally managed, influenced, quality checked and processed by the highly trained and precision-skilled hands of Sealy employees.
Locally hand-made at scale
Sealy offers beds that range from entry-level to high-end luxury, and each one is made here in Australia. “We see hand-made in Australia as a badge of honour and we do our best to live up to our goal of making the highest quality Australian-made products at every price range,” says Britta Gehrman, Sealy Australia’s Design Innovation Manager.
“Our materials are very much Australian sourced, Australian designed, Australian hand-sewn, and tailored-for-you by Australian employees. We have a premium image in the marketplace, underpinned by pure Australian craftsmanship.
With timber sourced from Maryborough in Queensland, steel gauge wire sourced from Australian suppliers and fabrics from Victoria, it’s very much a national affair. Even though raw materials are sourced throughout the country, it’s the refinement and manufacturing alchemy that happens at Sealy HQ which turns unassuming timber, steel, wool and other fibres into bedding gold.
As Garry Walshe, a Production Manager at one of Sealy’s manufacturing facilities points out, the details are everything when it comes to Sealy beds. “Our manufacturing plants produce the world’s best quality beds … We focus on the little particulars customers tend to notice, like labels being stitched on perfectly or what colour threads we use.”
He adds, “consumers may expect that Sealy only uses computers and machines to make your bed. They’d be surprised by how involved and manual our processes really are. There are 11 sets of hands that each bed will go through: quilting, overlocking, spring unit, UniCasing, borders and gussets, build, tape edging, handles, quality, packaging, then dispatch.”
“We pair innovation and hand-made quality with the desire to want to get beds to consumers the second they order one. Our ability to do what we do combining high-touch with speed is what gives us our competitive advantage.”
Design that raises the bar
Sealy’s Design and Innovation Team is well aware how maintaining a competitive advantage makes a difference to consumers: “we know your bed will be a part of your home for the next 8 to 10 years, so we look at the trends and influences that drive interior design now and into the future. We believe that each time you change the sheets, the beautiful fabric covering the mattress (or ‘tick’ in industry parlance) makes a statement about the quality and care that go into making that mattress. So we scrutinize every design choice to ensure it will live up to Sealy’s reputation for high quality, modern yet timeless design,” explains Britta.
She continues, “we have had customers contact us to comment on how beautiful their beds are — it makes us incredibly proud to be able to provide a moment of delight in people’s lives.”
Much like retailers offer different fashion or accessory collections, Sealy mattress ranges also reflect an aesthetic that will uniquely represent their market presence. The Sealy team works closely with buying teams to tailor their ranges: each retailer selects their new Sealy ‘look’ from a range of options, then Sealy crafts the collection including criteria such as design elements, colour, and accessories. This does mean a large number of different fabrics have to be meticulously designed, refined and then thoroughly tested before being released to market.
Tailoring design to suit you
Not every sleeper suits the same bed, and not everybody likes the same aesthetic. With the understanding that a bed is a very personal purchase, Sealy does its utmost to provide a personalised sleeping experience, designed to suit any home and anyone. Every detail is considered, right down to the colour of the stitching colour on the mattress. According to Britta, the base of the bed plays a big part in the scheme now, too.
“We’ve developed a whole suite of colours that you can choose to personalise your base to suit your home … In the fabric swatches we do have some decorator foundation options where people can choose to personalise it for their environment,” she says.
But it’s not just about a personalised aesthetic that can stand the test of time, it’s about the physical needs of the consumer. So, in addition to personalising your colour choices, you also choose your level of comfort and support.
Garry gives us another view of Sealy’s focus on personalisation from the front line. “If you go to a retailer on the weekend and buy a premium Sealy Posturepedic bed, we’ll build it for you. It’s the ultimate in personalisation. You don’t have to guess how long it’s been in a warehouse. Raw material components come in the bedding plant daily. Our foam order comes in at 6 o’clock for that day’s build but only enough for what we need. We don’t warehouse our components; we don’t warehouse our finished products,” he says.
“So while you may not think of your bed as bespoke to you, that’s what we offer — made for you, by us, only after you purchase a Sealy bed, hand-made with ‘end to end attention’ right here in Australia.”